Introduction
AMDEC (Analyse des Modes de Défaillances, de leurs Effets et de leur Criticité ou, en anglais, FMECA/FMEA : Failure Mode Effects and Criticality Analysis) est une méthode inductive (cause –> conséquences) qui permet de réaliser une analyse qualitative et quantitative de la fiabilité ou de la sécurité d’un système, d’un processus ou d’un produit.
La méthode AMDEC est développée initialement par l’armée américaine. La référence Militaire MIL-P-1629, intitulé « Procédures pour l’Analyse des Modes de Défaillance, de leurs Effets et de leurs Criticités, est datée du 9 Novembre 1949.
A partir des années 60, la méthode a été employée pour la 1ère fois dans le domaine de l’aéronautique pour l’analyse de la sécurité des avions.
A la fin des années soixante-dix, la méthode fut largement adoptée par Toyota, Nissan, Ford, BMW, Peugeot, Volvo, Chrysler et d’autres grands constructeurs d’automobiles.
Bien qu’ayant subi de nombreuses critiques dues au coût et à la lourdeur de son application, elle reste néanmoins une des méthodes les plus répandues et l’une des plus efficaces. Elle est en effet de plus en plus utilisée en sécurité, maintenance et disponibilité non seulement sur le matériel, mais aussi sur le système, le fonctionnel et le logiciel.
Définition des termes relatifs à la méthode AMDEC
Défaillance
Une défaillance se présente lorsqu’un produit, un composant ou un ensemble : Ne fonctionne pas, ne fonctionne pas au moment prévu, ne s’arrête pas au moment prévu, fonctionne à un instant non désiré ou fonctionne, mais les performances requises ne sont pas obtenues.
Modes de défaillance :
La façon dont un produit, un composant, un processus manifeste une défaillance ou s’écarte des spécifications. Ce mode peut prendre l’une des formes suivantes : Une déformation, vibration, coincement, desserrage, corrosion, fuite, perte de performance, court-circuit, flambage, difficulté à s’arrêter ou à démarrer, dépassement de la limite supérieure tolérée, etc. Les modes de défaillance sont parfois décrits comme des catégories de défauts.
Un mode de défaillance potentiel décrit la façon dans laquelle un produit ou un procédé pourrait échouer dans l’exécution de sa fonction première.
(Modes de défaillance en AMDEC == Dépassement d’une limite critique en HACCP)
Causes de défaillances :
Les causes de défaillances (amont) sont les circonstances associées à la conception, à la fabrication ou à l’utilisation, qui ont entraînés une défaillance.
Effets de défaillances :
Les effets de défaillances (aval) sont les symptômes par lesquelles est décelée l’altération ou la cessation d’une fonction requise, et qui en est la conséquence sur le client (le client peut être le consommateur ou un autre processus).
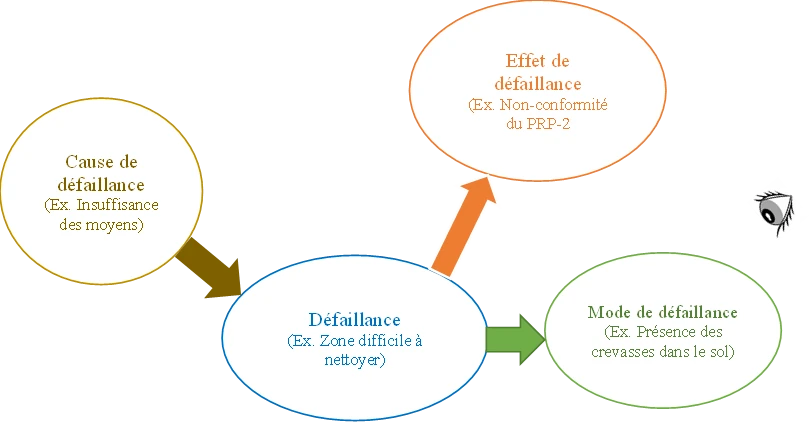
Le tableau ci-après illustre un exemples de défaillance, mode de défaillance, effet de défaillance et cause de défaillance.
Mode de défaillance | Défaillance | Effet de défaillance | Cause(s) de défaillance |
Présence des crevasses dans le sol. | Zone difficile à nettoyer | Non-conformité du PRP-2 (Disposition des locaux) | Insuffisance des moyens |
Boite de conserve bombée. | Produit non sûr ou NC. | Porter préjudice à la santé du consommateur. | Traitement thermique insuffisant ; Etanchéité. |
Développement du C. botulinum. | Produit non sûr ou NC. | Porter préjudice à la santé du consommateur (mort). | Barème de stérilisation inadéquat. |
Types AMDEC et leur utilisation
Il existe plusieurs types AMDEC selon l’usage prévu :
AMDEC produit
Utilisée pour étudier en détail la phase de conception d’un produit afin de vérifier sa fiabilité par rapport aux exigences du client (Elle sert à assurer la fiabilité d’un produit en améliorant sa conception).
AMDEC processus
Permet d’analyser les processus de la fabrication qui peuvent mener à un risque, mener à des produits non conformes, ou encore une perte de production dans le processus. Elle permet de mettre clairement en évidence les défaillances engendrées par les processus. Elle permet aussi d’étudier les problèmes dus aux postes de travail par exemple.
(Assure la qualité d’un produit en améliorant les opérations de production de celui-ci).
AMDEC moyen
S’applique à des machines, outils, équipements et appareils de mesure, des logiciels et systèmes de transport interne.
(Elle assure la disponibilité et la sécurité d’un moyen de production en améliorant sa maintenance).
AMDEC sécurité
S’applique pour assurer la sécurité des opérateurs dans les procédés où existent des risques pour ceux-ci.
AMDEC flux
Permet d’anticiper les risques liés aux ruptures de flux matière ou d’informations, les délais de réaction ou de correction, les coûts inhérents au retour à la normale.
Chacun de ces types d’AMDEC donne en sortie un document de travail pour la suite du développement, par exemple :
- pour l’AMDEC produit, un plan de fiabilisation ;
- pour l’AMDEC processus, un plan de surveillance, contrôle qualité ;
- pour l’AMDEC moyen, plan de maintenance préventive ;
- pour l’AMDEC flux, le plan de sécurisation des stocks.
- Pour l’AMDEC sécurité, le plan de sécurité des opérateurs.
Principes généraux de la méthode AMDEC
L’idée principale d’AMDEC est d’identifier les modes de défaillance, de définir les causes probables, d’évaluer les effets secondaires et donc, prévoir les actions préventives ou correctives. Ainsi, les études réalisées dans ce cadre sont de deux types : quantitatives et qualitatives.
L’étude qualitative consiste à identifier toutes les modes de défaillances possibles, leur effet sur le client et les causes de ces défaillances.
L’étude quantitative consiste à estimer la criticité (C) associée à chaque mode de défaillance. L’évaluation de la criticité, appelée aussi Niveau de priorité de risque (NPR) ou indice de priorité de risque (IPR), passe par l’estimation de 3 critères :
- Gravité (G) :
La gravité (ou la sévérité) est une évaluation de l’importance de l’effet de la défaillance potentielle sur le client (le client peut être le consommateur ou un autre processus).
La gravité n’est applicable qu’aux effets. Elle généralement est côté de 1 à 5 ou de 1 à 10.
- Fréquence d’apparition (F) :
La fréquence d’apparition est une évaluation de l’occurrence d’une défaillance. Elle est généralement cotée de 1 à 5 ou de 1 à 10.
- Détectabilité (D) :
La détectabilité est le risque associé à la non-détection de la défaillance. Elle est généralement cotée de 1 à 5 ou de 1 à 10.
Cotation | Gravité (G) | Fréquence (F) | Détection (D) |
1 | Inexistant | Faible | A l’œil nu |
2 | Désagrément | Moyenne | Par un examen simple |
3 | Hors norme | Fréquent | Par un examen détaillé |
4 | Dangereux | Très fréquent | Par une analyse |
5 | Mortel | Tous le temps | Indétectable |
- Criticité (C) :
La criticité (C) est le produit des trois grandeurs (GxFxD). Ce dernier sert à hiérarchiser les défaillances selon l’importance du risque.
C = FxGxD
Après une hiérarchisation des défaillances potentielles, basée sur la criticité, des actions prioritaires sont déclenchées, réalisées et suivies.
Étapes de mise en place de la méthode AMDEC
Avant d’entamer la mise en place proprement dite de l’AMDEC, il faut satisfaire certaines conditions préliminaires considérées comme essentielles pour la réussite d’une analyse AMDEC.
Conditions préliminaires
L’utilisation de l’AMDEC nécessite au préalable :
- Formation de tous les acteurs potentiels et de l’animateur de l’équipe.
- Formation de l’équipe à l’utilisation des outils de travail de groupe (Pareto, Ishikawa, etc.).
- Désignation d’un pilote pour les actions AMDEC, directement rattaché à la direction.
- Prévoir les moyens nécessaires : L’analyse AMDEC nécessite beaucoup de temps (8 à 40 heures, voir plus) pour chaque intervenant ou participant, et le double pour l’animateur.
- Disponibilité des membres de l’équipe.
- Rigueur pour le respect de la procédure de référence et suivi des actions correctives.
Principales étapes de la mise en place de l’AMDEC
Les principales étapes de la mise en place d’une démarche AMDEC sont les suivantes :
- Poser le problème : Définir clairement l’objectif à atteindre et le champ d’application.
- Définir le demandeur et le décideur : Le demandeur peut être, par exemple, le client qui cherche à s’assurer que tous les risques sont identifiés. Le décideur, c’est le chef du projet qui accepte ou non les exigences du client et identifie le sujet, le délai et le budget alloué à l’étude.
- Constituer l’équipe AMDEC : L’équipe doit être pluridisciplinaire et elle est composée de l’animateur, qui est le garant de la méthode AMDEC, et de représentants des différentes fonctions concernées. Il est préférable que l’animateur ne soit pas le concepteur du processus (ou autre) objet de l’étude.
- Analyse fonctionnelle : Le système est décomposé en sous-systèmes, et ceux-ci en composants élémentaires. Pour chaque élément on détermine les fonctions principales (à quoi ça sert) et les fonctions contraintes (lois, règlements, normes, etc.). La fonction est formulée sous forme verbale : Un sujet et un verbe.
- Analyse qualitative des défaillances : Recensement des modes de défaillance, des causes qui sont à l’origine (Causes de défaillance) et de leur effet (Effet de défaillances).
- Analyse quantitative des défaillances : Pour chaque mode de défaillance, évaluer la gravité, la fréquence d’apparition, le risque de non-détection et calculer le nombre prioritaire de risque (NPR).
- Déterminer le NPR critique : Après la hiérarchisation des modes de défaillance selon leur NPR, on détermine le NPR au-dessus duquel il faut déclencher des mesures correctives.
- Plan d’action : Préparer un plan d’action (quoi, qui, comment, quand) pour supprimer les causes de défaillances. Les actions peuvent être d’ordre préventif et/ou correctif.
- Application et suivi du plan d’action : Les responsables désignés sur le plan d’action sont chargés d’appliquer et suivre les mesures correctives et/ou préventives et d’enregistrer les résultats obtenues.
- Vérification de l’efficacité des solutions : La mise en œuvre des solutions est suivie d’une vérification de leur efficacité. Au cas où les solutions ne permettent pas d’atteindre les effets escomptés, il faut reprendre une nouvelle analyse et définir de nouvelles solutions.
Exemple AMDEC
L’exemple suivant est une illustration simple d’une AMDEC moyens. L’équipement concerné par l’analyse AMDEC est la « cisaille guillotine motorisée ».
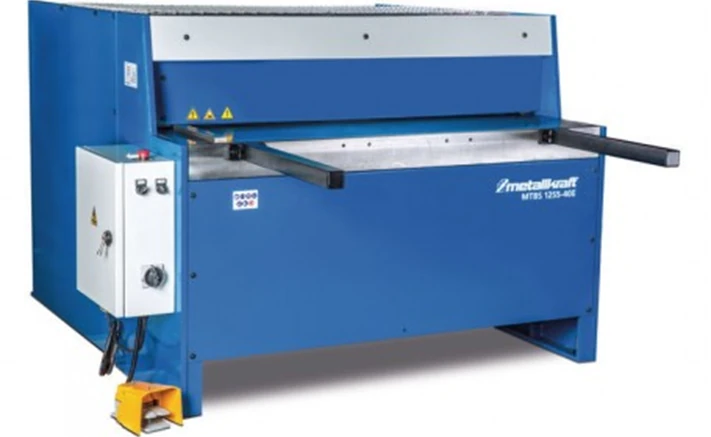
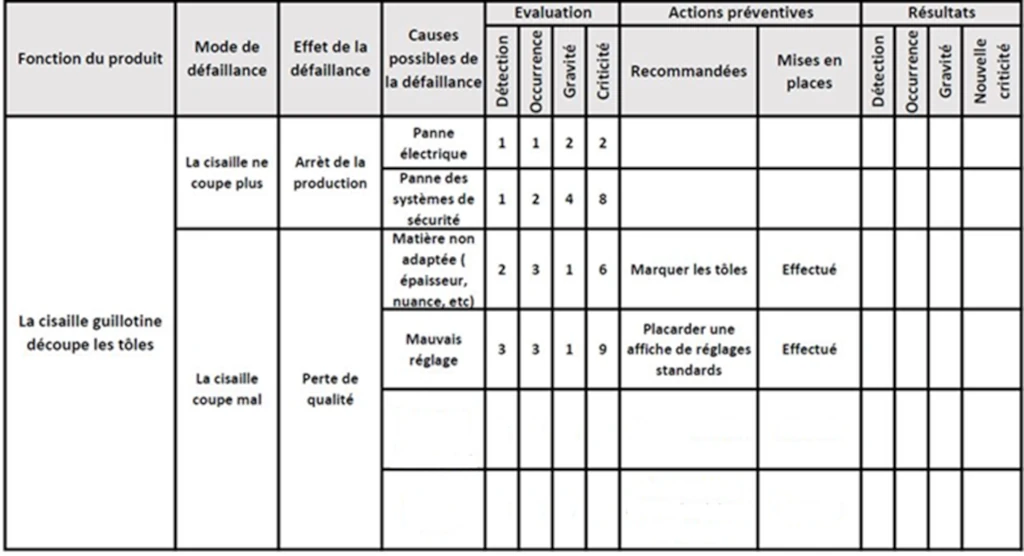